Amish Crafted Garden Lighthouse Manufacturer Tour
Did you ever wonder how Amish crafted garden lighthouses are made? We asked one of our Amish manufacturers to give you an insiders look at how the process works. Our host will be the Kauffman family, owners of Beaver Dam Woodworks located in the rolling hills of scenic Chester County, Pennsylvania. As many Amish businesses are, they are a "home-based" wholesale business serving retailers since 1998.
The Early Years
Amos Kauffman gives us a peek into the past as he reminisces of his days working for a gazebo manufacturer. He is grateful for an opportunity the management provided him and the other employees. Employees were permitted to manufacture items in their shop at home and bring them along to work to sell to their employers clients. This arrangement gave Amos a start in the nautical decor business.
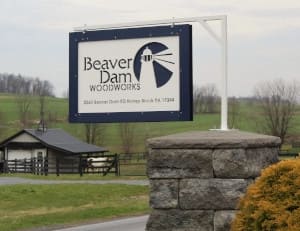
In the early days Amos focused almost entirely on interior decor, including rowboat bookcases and bookshelves. However the interior focus was short lived as more and more requests came for garden lighthouses in a vast assortment of sizes and colors. Almost before he knew what was happening, what started as a side hustle, became a fulltime business.
Amish Owned & Operated
Having a business of your own, located on your property is a goal for many Amish families. This allows for the trade skills of one generation to be passed to the next as a father and his children work side by side day after day. More importantly as a father spends quality time building strong relationships with his children he passes on his faith in a tangible way.
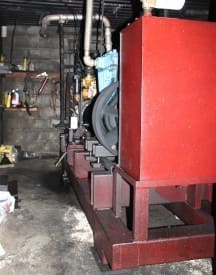
Off The Grid
In 1998 Beaver Dam was born and 24 years and well over 100,000 garden lighthouses later Amos and his family are still producing nautical masterpieces. We begin our tour in the rear of the shop where there is an engine room. As many of you know, Amish live "off the grid", their homes and shops are not powered by a local power company like MetEd or PP&L.
While Amish homes generally have no electricity, their businesses are often powered by a diesel genset which powers air, hydraulic, or electric tools. Lighting is often a combination of large windows, skylights, and traditional gas lighting. In select locations you made find lights powered by battery as well.
While this may not be the most cost effective source of power, Amish adhere to their decision to live off the grid. Their decision has its roots in religious conviction to live a simple life, consecrated to God, and separate from society at large.
Building Garden Lighthouses
Raw materials are purchased in truckload quantities to provide the consumer a quality product at the lowest cost possible. In the rear of the shop is a lumber yard where lumber is stored on racking until it is needed. Here we find a mixture of traditional wood lumber, high grade exterior/treated wood lumber, poly lumber, and woodgrain premium poly lumber. Lumber is brought into the rear of the shop where it is sorted by type, size, and color, then placed in close proximity to a chop saw.
The craftsman running the chop saw pulls lumber for that weeks production and begins the process of cutting each piece to length, using a jig to precision cut the bevels and angles. Sanders and jointers are used to make sure each joint will fit snug, preventing moisture from getting inside the lighthouse.
Air nailers and screw guns are used for assembling the components of the lighthouse. All fasteners are stainless steel to prevent rust.

Finishing Garden Lighthouses
Wood lighthouses and lawn decor items are given several coats of exterior grade paint to seal out any moisture that a driving storm may try to force inside. This is done in a spray booth to ensure an even, protective coat is applied to all exposed surfaces. After several coats of finish are applied, the lighthouses and parts are stacked to dry.
When the paint has cured final assembly begins:
Lighthouses have decorative plastic windows and doors fastened with a Brad nailer.
Roof finials are inserted in the roof and secured.
Plexiglass panes are inserted and secured in the lighthouse top.
The customers lighting option of choice is installed in the top.
Packing For Shipping
After final assembly each lighthouse is given a final inspection and then wrapped in several layers of shrink wrap to protect the finish during shipping. The roof and top on larger models is wrapped separately and placed inside the lighthouse tower for protection during the shipping process. A piece of plywood is secured to the bottom of the lighthouse to keep the roof and/or top secure inside the tower, while also keeping the lighthouse in the center of the shipping box to prevent damage from blows administered to the side of the carton.
The lighthouse is now ready to head down the elevator to the shipping department. Lighthouses are packed in shipping cartons and labeled for UPS to deliver. Larger models are shipped via Freight carriers.
Video Coming Soon!